Symulacja procesu tłoczenia — sposób na minimalizację kosztów
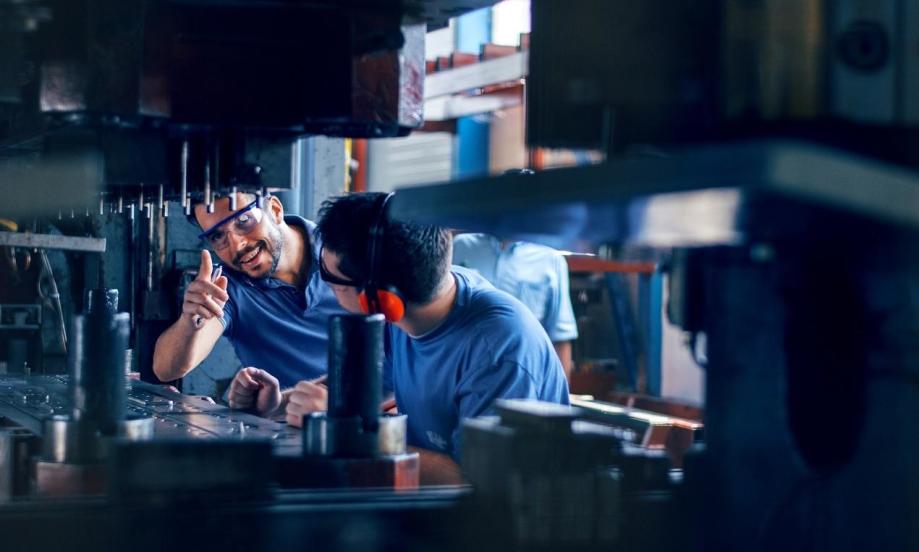
Projektowanie wyrobów z blach jest procesem, w którym należy uwzględnić duże ryzyko konieczności wprowadzania nagłych zmian. Ewentualne poprawki wydłużają czas produkcji, który mógłby być przeznaczony na wytworzenie innych elementów i sprzedanie ich z zyskiem. Symulacja tego procesu umożliwia sprawdzanie poszczególnych produktów, jeszcze przed ich ostatecznym wyprodukowaniem, a wiec bez ponoszenia zbędnych kosztów.
Istota symulacji
Konieczność przeprowadzenia symulacji procesu tłoczenia wynika z faktu, iż w procesie produkcji powstaje wiele wad wyrobu, np. fałdowanie, pękanie, niewłaściwa jakość powierzchni, błędy w zakresie wymiarów. Podejmowane działania mające na celu wyeliminowanie wadliwej produkcji, są kosztowne i czasochłonne, stąd konieczność testowania produktów jeszcze przed ich ostatecznym wytworzeniem.
Symulacje wykonywane w oparciu o specjalistyczne oprogramowanie komputerowe pozwalają na stosowanie odpowiednich algorytmów optymalizacji. System taki daje możliwość ilościowego i jakościowego opisania produktu gotowego, a dzięki temu można zminimalizować ilość nieudanych prototypów. Firma ZETEK sp. z o.o. stosuje software PAM STAMP oraz AUTOFORM, które pozwalają na kompleksową analizę realizowanego procesu przemysłowego.
Zalety symulacji procesu tłoczenia
Symulacja procesu tłoczenia pozwala na dokonanie oceny wykonalności poszczególnych części, zaprojektowanie tych elementów oraz całkowitą symulację weryfikacyjną. Konstruktor może dzięki temu przewidzieć, jak będzie się zachowywał materiał w trakcie kolejnych etapów tłoczenia. Dzięki temu możliwe jest zoptymalizowanie procesu, by na jego końcowym etapie otrzymać dany detal bez skłonności do pękania, fałdowania bądź zbyt dużego sprężynowania.
Symulacja procesu tłoczenia niesie za sobą konkretne korzyści. Są to:
- optymalizacja liczby wykonywanych operacji i całego procesu tłoczenia,
- możliwość weryfikowania poszczególnych czynności i efektów na etapie projektowania,
- minimalizacja kosztów,
- precyzyjne odwzorowanie produktu,
- analizowanie błędów i niedoskonałości oraz ich wyeliminowanie,
- łatwe i szybkie nanoszenie ewentualnych poprawek,
- skrócenie czasu uruchomienia produkcji,
- uruchomienie procesu wytwarzania za pierwszym razem,
- redukcja liczby dokonywanych napraw.
Stosowane w symulacjach programy komputerowe umożliwiają zaprojektowanie oraz wytworzenie zróżnicowanych, skomplikowanych produktów, przy jednoczesnym minimalizowaniu kosztów tego procesu.
Dziękujemy za ocenę artykułu
Błąd - akcja została wstrzymana
Polecane firmy
-
Rafał Gomułka Zakład Ślusarsko Mechaniczny
Metale - obróbka, maszyny
woj. małopolskie33-114 Świebodzin 48